UpNano GmbH (Vienna, Austria) has co-developed a novel manufacturing process for 3D-printed fused quartz objects. This innovative technology enables the production of high-precision shaped parts in the mm and cm-range. The process is based on Glassomer GmbH’s (Freiburg, Germany) innovation and has been modified for two-photon polymerisation (2PP) 3D-printing using UpNano’s NanoOne high-resolution printing system. These are the highest performance 2PP 3D-printers on the market, capable of printing over 15 orders of magnitude.
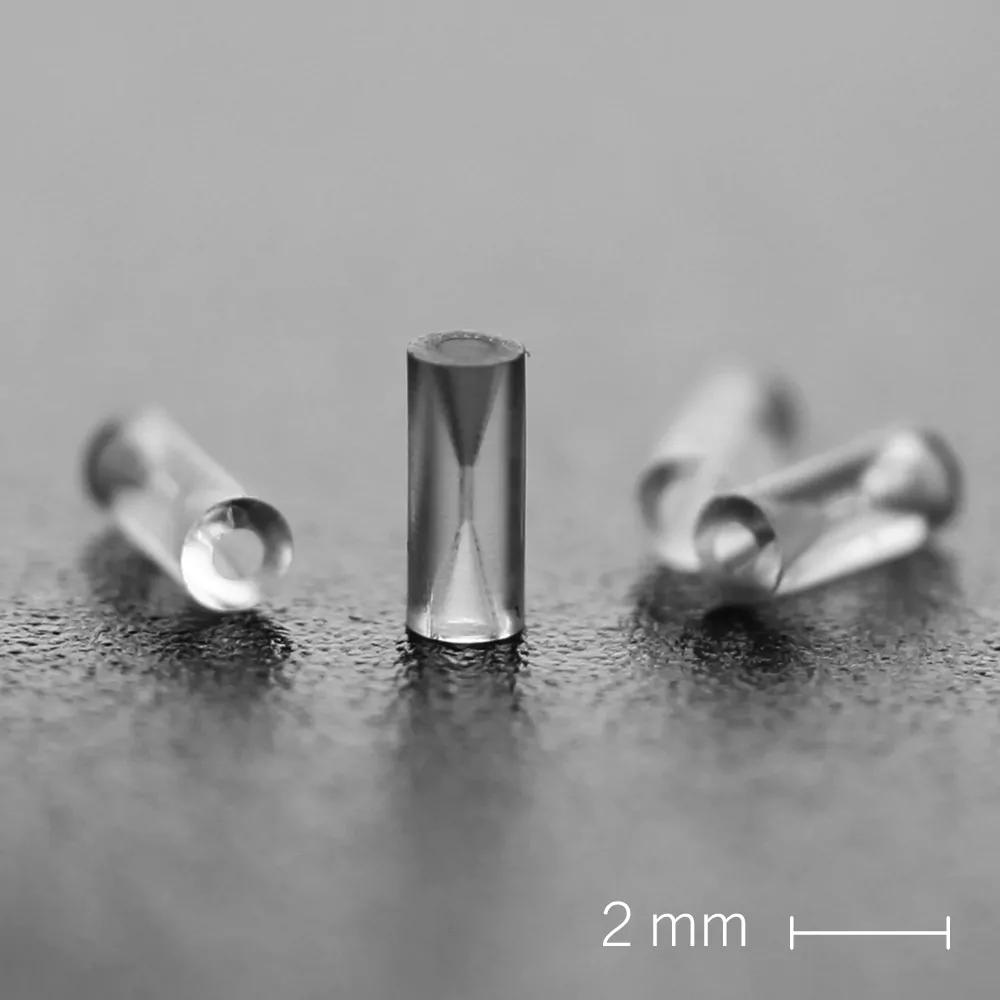
Fused silica ferrules with inner diameter of 126 µm matching the outer diameter of standard glass fibers. Such ferrules are generally used to mount and connect bare optical glass fibers. Due to the low and perfectly matched thermal expansion coefficient of the fused silica ferrule and optical glass fiber, UpQuartz is an ideal material for this application.
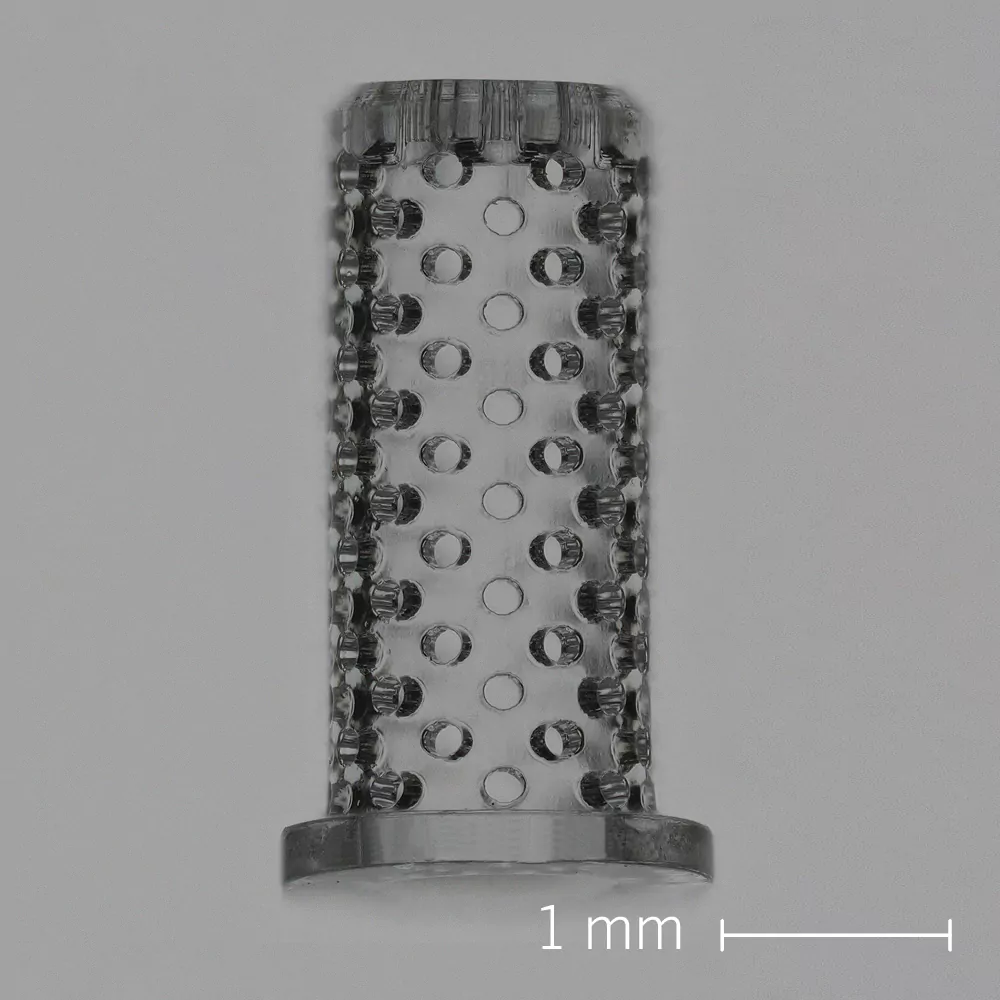
Fused silica filter-element with 180 µm pores. The filter is 3.6 mm long and has an inner diameter of 875 µm. The device is equipped with a rim for mounting. The filter element has a high temperature resistance and can withstand extremely harsh chemical conditions, as it is made of fused silica glass.
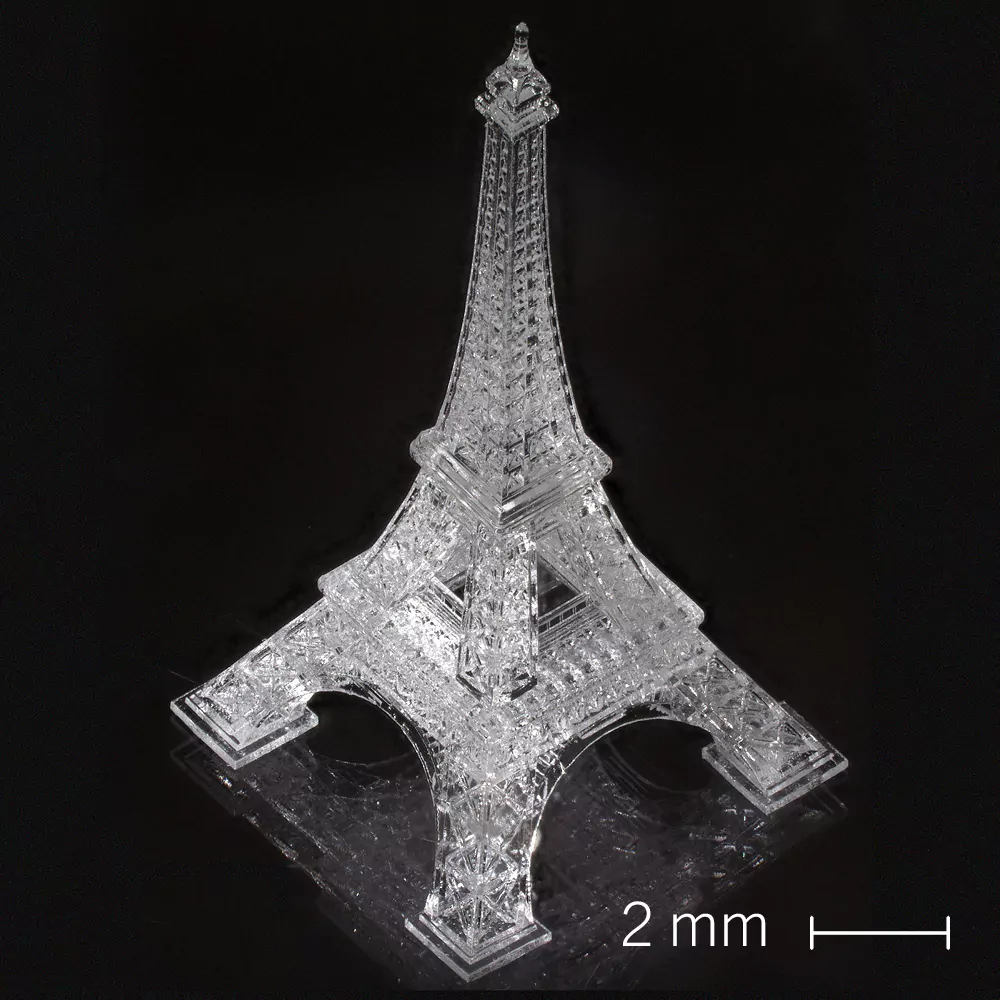
Eiffel Tower, directly printed from UpQuartz, showcasing the obtainable complexity as well as remarkable size that can be achieved with UpQuartz. The tower is 10 mm high and has intricate features that reach into the tens of micrometers range.
Manufacturing minuscule and complex 3D objects in glass is a challenging process. This is even more the case, if the required material is to be high-quality fused silica (SiO₂) glass, which has an exceptionally high melting point. The only possible methods that can be used are based on non-commercially available equipment and include melting glass fibers using laser beams or fused deposition modeling to produce soda lime glass. These methods often result in final products with rough surfaces that are undesirable. Now, UpNano and Glassomer have developed a rapid 3D printing process to produce smooth fused silica parts in the mm and cm range with features in the μm range.
A 3-Step Process
“It’s a three-step process”, explains Markus Lunzer, team lead of Materials & Application at UpNano. “The first step is to design and print the desired structure using all the advantages 2PP 3D-printing offers. The second step is to remove organic binder material followed by a high temperature sintering process, the third step.” At the core of this is a newly developed nanocomposite “UpQuartz”. In addition to SiO2 nanoparticles, it contains a specially designed polymer matrix that allows the composite to be 2PP 3D-printed in the first place. The printing process produces a “green part” that already has the shape of the final and desired structure. To obtain the fused silica product in the end, the polymer matrix must be removed. Heating the green part to 600°C effectively removes the polymer matrix, leaving behind the “brown part”. This is all SiO2 nanoparticles in the shape of the final product. The structure is sintered and fused after exposure to 1,300°C. During the post-processing, the object undergoes isotropic shrinkage of approximately 30%. This can easily be compensated for by an appropriate upscale of the green part using UpNano’s software.
“This innovative production process we developed”, says Markus Lunzer, “is ideally suited for larger 3D-printed glass parts that require high-resolution and high-precision, in the fields of engineering, and chemical, medical or research applications.” Fused silica offers superior optical properties, along with biocompatibility as well as high chemical inertness and exceptional heat resistance, making it an ideal material for a vast range of applications. This new development marks a significant advancement in the potential of 2PP 3D printing, following UpNano’s recent success in advancing the material testing of 2PP 3D-printed parts using UpNano printers and resins for macroscopic test specimens. In addition, the company’s printers have recently been used to achieve a significant milestone in 2PP 3D-printing by producing holistic embedded microfluidic chips as well as tungsten and platinum microstructures with (sub-)μm resolution.
The production of fused silica objects by 2PP 3D printing was a joint development between UpNano and Glassomer. The German company has previously enabled the production of fused silica objects by employing technologies such as soft lithography, injection molding, as well as conventional 3D-printing. Now, the joint material development from UpNano and Glassomer also allows the use of high-precision 2PP 3D-printing to produce fused silica objects.
Capital Investment
This series of developments exemplifies UpNano’s innovation capital in the highly competitive 2PP 3D-printer market, complemented by the continued and growing commercial success of the NanoOne printer range. In fact, sales in 2023 were up 57% on the previous year and customers are now served on five continents. All NanoOne printers are equipped with patented adaptive resolution technology, which allows the laser beam to be expanded by a factor of 10 for any given objective. A recent software update has enabled seamless stitching, and given all the available modules, the NanoOne range of printers now is considered the most versatile and fastest 2PP 3D-printer on the market. “The speed, resolution, and versatility of our printers make them powerful tools for the mass production of highly precise parts. Our ever-expanding range of materials extends the range of applications. In due course, we will also expand the range of services we offer”, adds Bernhard Küenburg, UpNano’s CEO.