COVID-19 and Adapting to Change
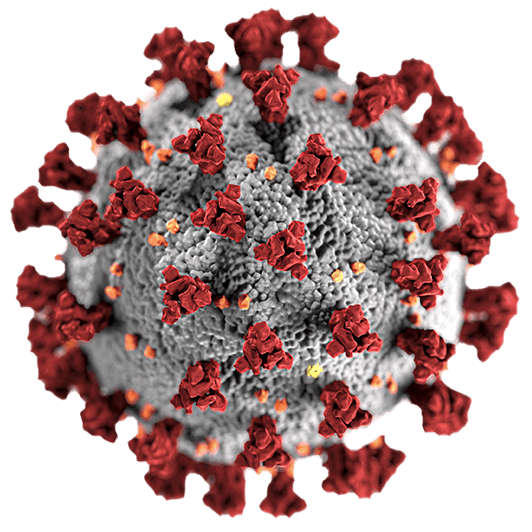
The current COVID-19 climate has made doing business the traditional way very difficult, and the way that we do business in the future will probably never return to the way it was pre-pandemic.
Suppliers of scientific instrumentation have been hit hard by travel restrictions and border closures making support internationally impossible and even interstate difficult. For AXT, adapting to these changes was only possible because of the strength of our local service capability and the expertise of our local team. We have had to adapt, but having support in all the major centres has provided continuity to our customers.
The Scientific Instrumentation Market
Sophisticated instrumentation is typically evaluated against three main categories. The technical criteria, the financial offer and service and support. The first two of these often overshadow the third core offering of Installation and ongoing service and support.
The specialised nature of scientific instrumentation makes installation and after sales service a crucial factor in the decision to purchase and COVID has highlighted the importance of strong local support services.
Recent Experiences
These recent experiences come from sales of high-end scientific instrumentation in Australia, but I am sure parallels can be drawn with other industries and geographies.
We are lucky to have a team of highly skilled engineers who are factory trained for various instruments. During the recent COVID-19 period, they have continued to install and service instrumentation around the country, albeit with slightly different modes of operation. This has resulted in uninterrupted operation for those customers still able to conduct business
To illustrate the point, I will provide three examples:
Example 1 – University of Western Australia Installation
We recently installed a Rigaku Oxford Diffraction Synergy-S single crystal X-ray diffractometer at the University of Western Australia. Our engineer who specialises in these instruments was locked down in Victoria when the installation was due to take place.
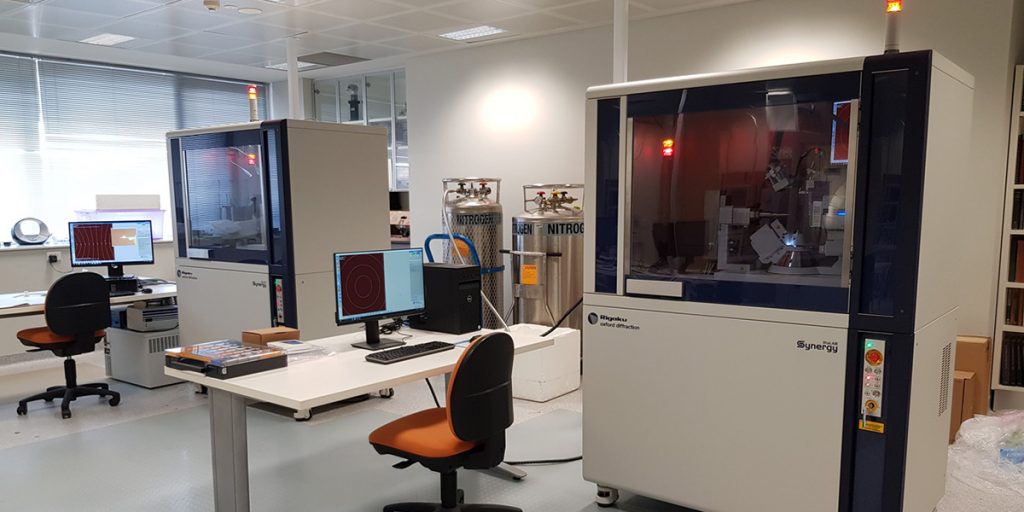
Fortunately, we were able to deploy local expertise from our Perth office. With assistance from Melbourne, the installation went smoothly. Follow-up training and technical support was also provided from Melbourne via video conference resulting in a seamless installation and commissioning procedure with no delays.
Our happy client Assoc. Prof. Stephen Moggach, was quoted as saying the following about our engineers who worked on his install:
Mark was an absolute star. Methodical, careful, considerate and professional. A lethal combination! If nothing else, that made purchasing a Synergy-S through AXT worthwhile. And the technical support from you Phil, as always, was amazing.
Assoc. Prof. Stephen Moggach, UWA.
Example 2 – University of Wollongong Installation
During the height of the COVID crisis we needed to install a NEXSA X-ray Photoelectron Spectrometer (XPS) from Thermo Scientific at the University of Wollongong. These are highly specialised pieces of equipment manufactured by only a few companies around the world, with installation typically carried out by engineers from the factory. However, with international flights cancelled, this was no longer a possibility.

Very few engineers from outside the factory will have any experience with servicing, let alone installation of an XPS system. Fortunately, one of our engineers had been involved with a couple of XPS installations over the recent years and was able to complete the install the system.
With commissioning and training able to be performed remotely from the factory, the customer was up and running on schedule with no delays due to COVID.
Example 3 – Queensland University of Technology Installation
Towards the beginning of the COVID-19 travel restrictions, we were due to install a TESCAN TIMA automated mineralogy system at QUT. With the drastic reduction in air transport the delivery was delayed with the system having to be delivered by sea freight. Our client was understanding of the delays, with university staff access limited as well.
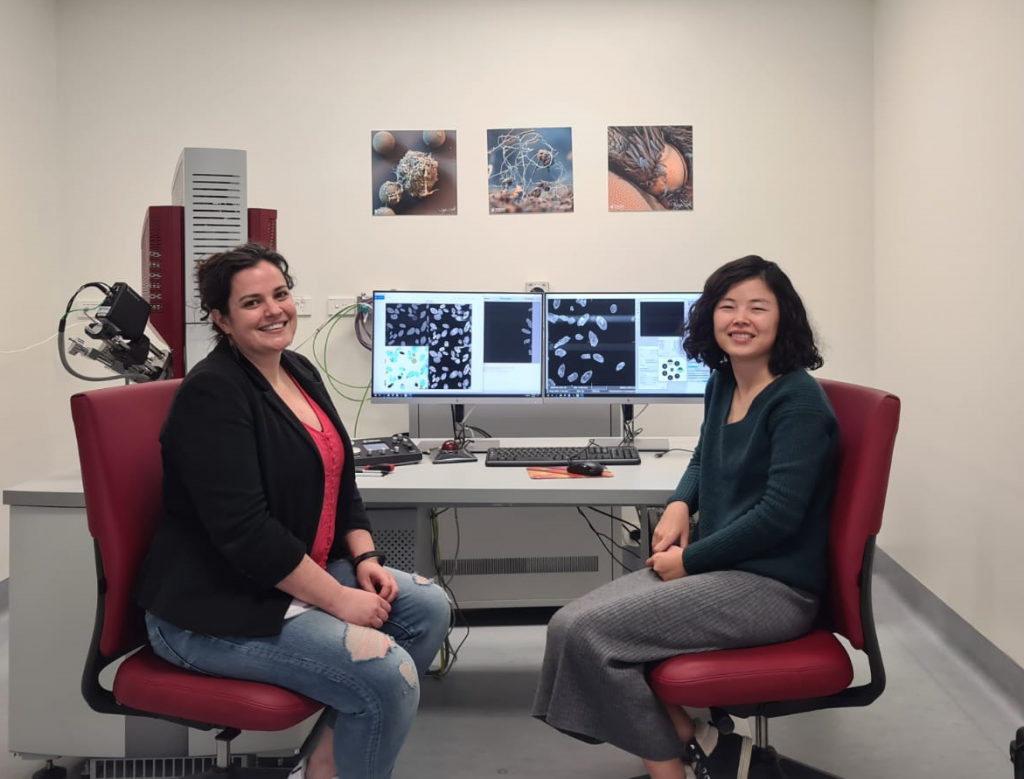
However, once the system arrived on site it was promptly installed by our local engineer whose work was praised by the client. Following passing acceptance tests, our experts in Perth, who have vast experience with the system and mineralogy were able to provide training remotely at times to suit the client, thus avoiding social distancing issues and travel restrictions.
This example of local service teamwork had the client up and running and collecting data in a very short period of time, extracting value from their investment.
Closing Note
There have still been impacts and delays due to COVID-19. Delivery times have been delayed due to a reduction in air transport. Local Institutes and even university services have been impacted which has also impacted timelines.
The bottom line is, due to the fact that we have field service engineers located around the country, our clients have experienced minimal delays in service compared to normal. The way that the service and training has been delivered may have differed slightly, but the fact that we have local operations has enabled us to provide excellent levels of service to our clients that would not have been possible if we did not have personnel on the ground. There have also even been instances where our engineers have been called up to provide services for other synergistic companies to help alleviate any delays due to travel restrictions, many of which still remain in place in Australia.
Furthermore, as some companies move their offices out of Australia, preferring to service Australia from Asia, the importance of local operations in supporting local clients has been highlighted during the pandemic