Metal 3D printing is an extremely exciting field with the ability to produce complex parts quickly and easily, when compared to more traditional techniques like casting or machining. It really comes into its own when small production runs are required.
The technique essentially fuses metal powders into the final shape using lasers, electron beams or cold spraying. Of these laser melting is the most commonly used method and the process may be known as Laser Powder Bed Fusion (LPBF), Selective Laser Melting (SLM), Direct Metal Laser Sintering (DMLS), Selective Laser Sintering (SLS) or even Direct Metal Printing (DMP).
LPBF systems range from compact desktop models, ideal for research and production of small components, through to larger system capable of industrial scale outputs. Manufacturers like Aconity3D have systems that span this range and cater for the needs of academia and industry.
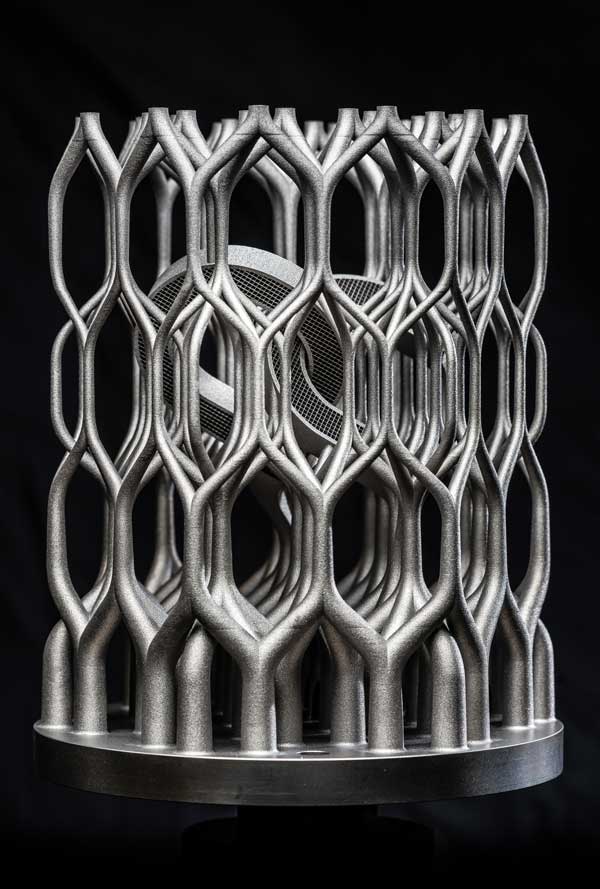
Features to Look For in a Metal 3D Printer
When buying a system you should look for a system that satisfies your performance requirements and offers versatility to allow you to take your 3D printing in any direction you might need in the future. With the design of parts almost limited only by your imagination, make sure the system you choose has as much flexibility as possible. Look for features such as:
- Completely free choice of all process parameters
- Control via Python API
- High powered, full overlap, multi laser options – fully modulated
- Multi-material options
- Platform heating
- Vibrating powder deposition
- Freely configurable machine
Other Useful Featuresto Look for in a Metal 3D Printer
Other features that could prove useful include:
- Multiple build chambers for maximum laser up time
- Vacuum option for reduced purging times
- High speed camera for process monitoring
- Coaxial pyrometry for recording of thermal emissivity