In Australia, the advanced manufacturing sector is booming. With the increasing implementation of additive manufacturing techniques, the need for non-destructive testing of complex components becomes even more important and computed tomography (CT) (Also known as microCT) is the go-to solution. Similar trends for CT are being seen in research, where there is a growing need to examine components non-destructively in 3D to optimise designs and fabrication processes.
There are currently a large number of solutions depending on what your requirements are and the choices can be confusing. We look at the various options that are available.

Sample Size and System Size
Benchtop systems are available for smaller samples, while larger systems can cater for samples in the meter plus range. Systems that cater for larger components may also include cranes and other lifting devices to aid loading as well as manipulators to manoevre the parts during examination.
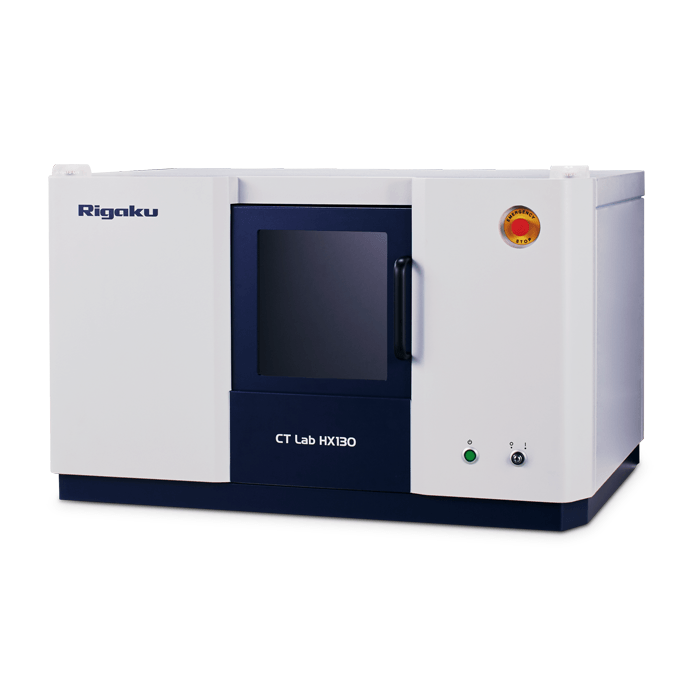
The Rigaku HX130 benchtop CT system.
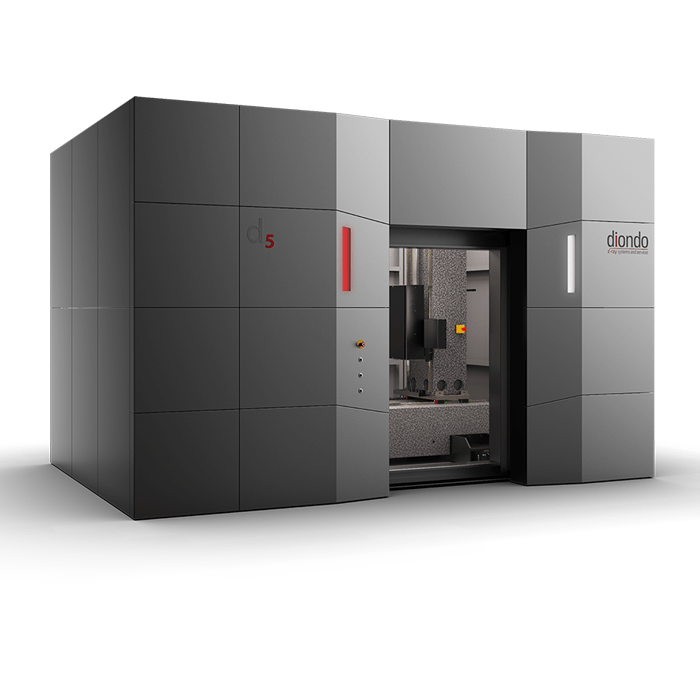
The diondo d5 highly configurable CT for components up to 100kg.
You should also take into account the availability of space in your lab or workspace. Some manufacturers like diondo offer compact systems that can be more easily integrated into smaller spaces e.g. into production environments.
Materials to be Examined
CT uses X-rays and X-rays are attenuated as a function of density and thickness. The penetrating power of a CT is dictated by its power i.e. kV. Systems up to 600kV are commonly available. For the largest, densest components, linac (linear accelerator) powered CTs are also available with power ratings up to 9MeV.
Lower power systems are more than suitable for imaging biological materials, organic materials, polymers, composites, ceramics and even thinner metals.
Imaging Modes
Oftentimes, the component being examined is made up of different phases. Depending on what they are e.g. differences in density, you may need to rely on different imaging modes to best resolve them to reveal any flaws or defects. These modes might include in quantitative phase contrast, bright field, dark field or phase retrieval. We will compare these imaging modalities in a future article.
Spatial Resolution
Depending on the size of the features and defects you are looking for, systems are available with sub-micron resolution using nano-focus X-ray sources and high resolution detectors.
Speed/Temporal Resolution
CT scans generate large datasets, with higher spatial resolutions, generating even larger datasets. Faster detectors and computers now allow for 360° scans in less than 10 sec, opening the door for higher throughputs and true dynamic (4D) scanning.

2D, 3D and 4D
CT is by definition 3D imaging. The ability to perform simpler 2D scans can also be a useful capability and can be a quick QC checking technique akin to radiography.
There is also a growing trend towards performing in situ studies within a CT. To do this successfully requires two things, the ability to incorporate a testing rig into the instrument (e.g. mechanical, thermal, environmental) that does not interfere with the imaging hardware and the ability to perform multiple scans, ideally on a continuous, uninterrupted basis generating real-time, 4D/dynamic imaging ensuring no instantaneous event e.g. fracture is missed.

System Flexibility
For the ultimate in flexibility, systems are available with different X-ray sources and detectors, sometimes with multiple installed side-by-side that can be easily swapped over depending on your specific requirement.
Investing for the Future
A CT system is a significant capital expense. Try and bear in mind what demands you may have in the future as this can give you added flexibility and extend or increase the useful service life of your instrument.
After Sales Support
Like any instrument, preventative maintenance should be performed periodically to ensure optimal performance. Make sure your supplier has a support network to facilitate both this and emergency service if required as well as a supply of spare parts e.g. filaments which are a consumable item, but essential to the operation of your CT.
Summary
AXT have Australia’s widest range of CT solutions from manufacturers such as diondo, TESCAN, Rigaku and Sigray. We also have access to the components and software needed to design and build custom solutions where the need arises. If CT technology is on your roadmap, please contact us to discuss your requirements.