Exaddon use a unique electrochemical additive micromanufacturing technology called µAM that allows them to produce metal structures in the 1 to 1000µm range with sub micrometer resolution. µAM can directly print complex structures such as springs, horizonal features or overhangs with no need for supports.
Their µAM technology is often an excellent alternative to existing techniques that involve deposition and subsequent etching. It has the advantage over these techniques in that it can directly produce these structures in a single process, and the resultant components is normally stronger and more robust.

How Does µAM Additive Micromanufacturing Technology Work?
A liquid containing metal ions is precisely delivered using a specially designed print nozzle called an iontip. The liquid travels through a microchannel in the iontip. The flow of liquid is precisely controlled by air pressure (as low as femtoliters per second).

As the liquid is delivered to the substrate, the dissolved metal ions are electrodeposited, forming solid metal. The deposited metal atoms grow forming voxels.
As each voxel forms the cantilever holding the iontip deflects similar to an AFM. Optical force feedback registers the completion of each voxel. This process continues until the entire component is complete.
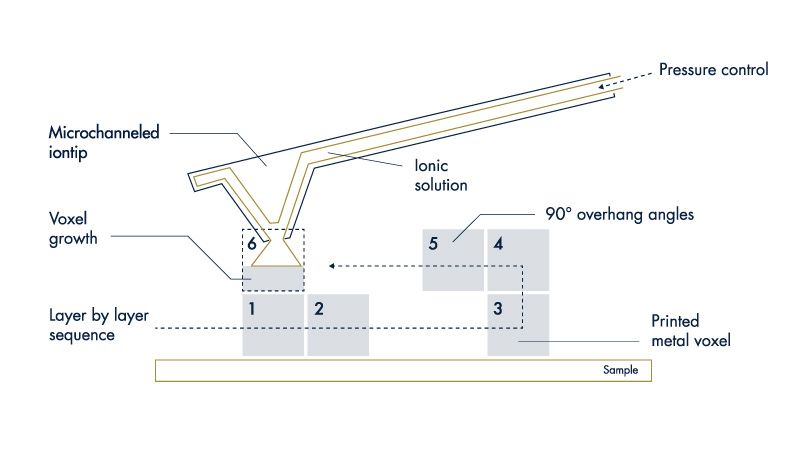
Final Products
The process produces high quality components that are immediately ready for use. No post-processing is required.
CERES has applications in both academic and industrial research, with applications in areas such as:
- High-frequency technologies
- Drug delivery microneedles
- Neuroprosthetics
- Semiconductor probe testing
- Semiconductors
- Fundamental research
- MEMS and packaging
- Microcoils and helix structures
- Watchmaking and copyrighting