One of the most challenging steps in materials research using electron backscatter diffraction (EBSD) technique is accurate sample preparation. The EBSD signal comes from the top few nanometers (approximately 20 nm) of the sample, which requires a very high-quality surface preparation. The sample surface must be free from contamination, oxidation, and, above all, crystal lattice damage (elastic strain) and plastic deformation (plastic strain).
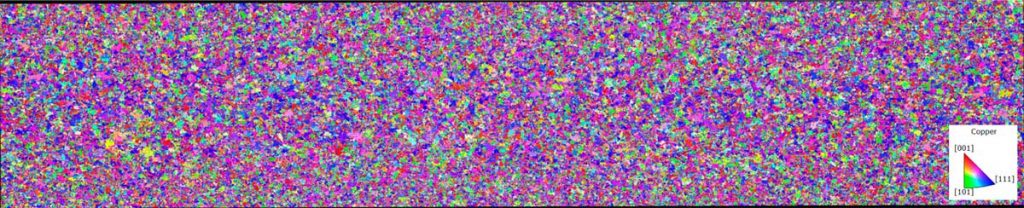
Several sample preparation techniques can be used to get high quality EBSD patterns, including mechanical polishing and electropolishing. While these techniques are accurate and yield good results, the techniques require several preparation steps and can be quite time consuming (more than ten hours, in some cases). Another limitation is that plastic strain can be introduced during mechanical grinding/polishing, which leads to degradation of EBSD pattern quality. Mechanical polishing can also cause dynamic phase transformation in austenitic steels or steels that contain retained austenite.
In the last decade, an emerging sample preparation technique for EBSD was argon broad ion beam milling (BIB). However, the most notable limitation of BIB technique is a relatively small milling area, which ranges from hundreds of micrometers up to 5 mm diameter.
We present here a development in large area sample preparation by BIB milling that offers uniform sample milling up to 50 mm in diameter. A milling area of this size is made possible by the user’s ability to position each of the tool’s three ion beams individually. This flexibility in ion beam positioning also enables more precise targeting of an area of interest.
Figure 1 shows an inverse pole figure (IPF) map of a 48 x 12 mm copper sample, uniformly milled across the entire area using the Model 1062 TrionMill [Fischione Instruments]. The sample was processed using successively 10 keV, 8 keV, and 6 keV beam energy at a 3° milling angle. The achieved high-quality polished surfaces allowed EBSD data acquisition at high speed (920 patterns per second) over a large area (5 cm), which revealed the microstructure of the copper sample with average grain size of 95 mm.
