Projection Micro Stereolithography or PµSL for short, is a micro 3D printing process that is a variation on stereolithography (SLA) that enables users to microfabricate components with ultra-high resolution down to 2 µm. With a range of commercially available liquid polymer resins and the ability to tailor your own formulation, PµSL introduces new levels of freedom compared to other traditional microfabrication techniques. It has the added benefits of superior material integrity and surface finish compared to conventional polymer 3D printing.
With many manufacturers across a variety of industries pushing for miniaturisation in their product designs, micro 3D printing opens new possibilities for component manufacturers, offering design freedom and rapid concept to product timeframes. While 3D printing and desktop 3D printers have become extremely accessible, sometimes design specifications go beyond their capabilities and even those of micro injection moulding and micro CNC machining. In this article we explore Projection Micro Sterolithography (PµSL) as an alternative solution.
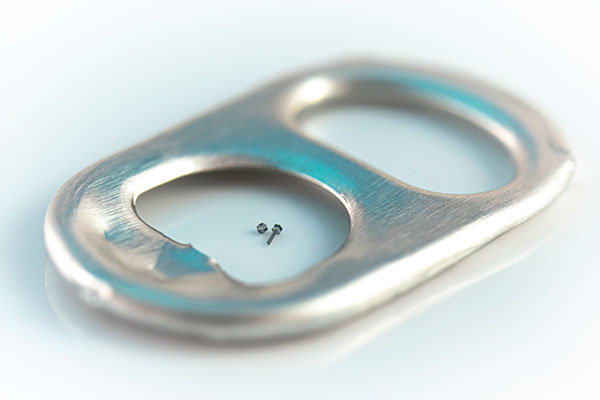
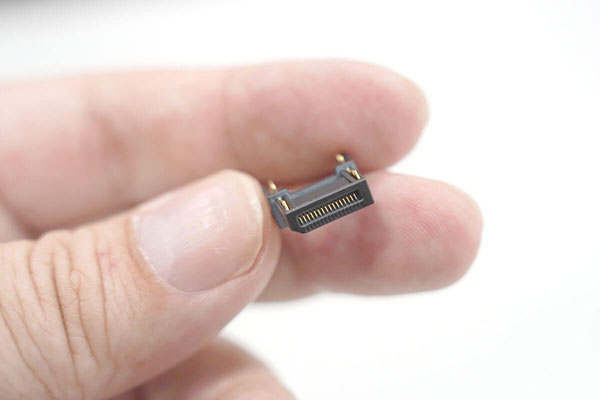
Examples of miniaturised components micro fabricated using PµSL technology, micro screws (left) and an electronic connector with fine holes through which countless metal terminals are passed (right).
Background
3D printing of polymers has really taken off in recent years. Interestingly, the driving force behind the growth has been non-commercial adopters or hobbyists who can get into 3D printing outlaying only a few hundred dollars, with systems available from any number of manufacturers and consumables being very affordable. That said, the ability to produce “rapid prototypes” has also seem industry also consume their fair share of 3D printers.
These highly affordable systems are based on Fused Deposition Modelling (FDM) or Fused Filament Fabrication (FFF). The process involves taking a thermoplastic polymer filament and extruding it through a heated nozzle. In doing so the polymer is melted and fused to the underlying later, effectively creating a 3D structure by depositing a series of 2D shapes.
While FDM can be used to print large components, small components and fine surface finishes are perhaps the Achillies heel of these systems. Another issue with FDM printing is the inherent weakness at the point where each layer comes together. While systems are being scaled up to produce larger components simply by increasing the travel of the gantry/print head, printing smaller components becomes a problem with nozzle diameters (typically of the order of 0.4 mm, and occasionally 0.2 mm) restricting with the level of surface finish they can achieve. So, what happens if you want to fabricate components with features smaller than that? What if you need high precision, high resolution and high accuracy?
While it is possible to produce some components by processes such as micro injection moulding, this process is suited to high volume production runs as the tooling can be expensive, especially where the component is complex. However. micro injection moulding may not be able to fabricate components with internal structures such as microfluidics. Similarly, micro CNC machining is limited by the size of the tools that can be used, low throughput rates and also the inability to form internal structures, although it can be ideal for applications such as low volume production of components with simple geometries.
There is a growing need to produce small components with surface finishes that rival micro injection moulding. This is where micro 3D printing technologies come in, with the ability to fabricate structures with features in the single micron range or even in the sub-micron range, potentially with internal structures and at volume.
Projection Micro Stereolithography
Projection micro-stereolithography (PµSL) is a form of stereolithography (SLA) that incorporates a DLP® light engine, precision optics, motion control and advanced software. SLA produces parts in layers using a photochemical process, whereby a photosensitive liquid resin is exposed to light so that polymeric cross-linking and solidification occurs. In contrast, the PµSL process, patented by Boston Micro Fabrication (BMF) marries the benefits of SLA and DLP technologies and employs a flash of ultraviolet (UV) light which results in the rapid photopolymerisation of an entire layer of resin. PµSL technology also supports continuous exposure for faster processing.
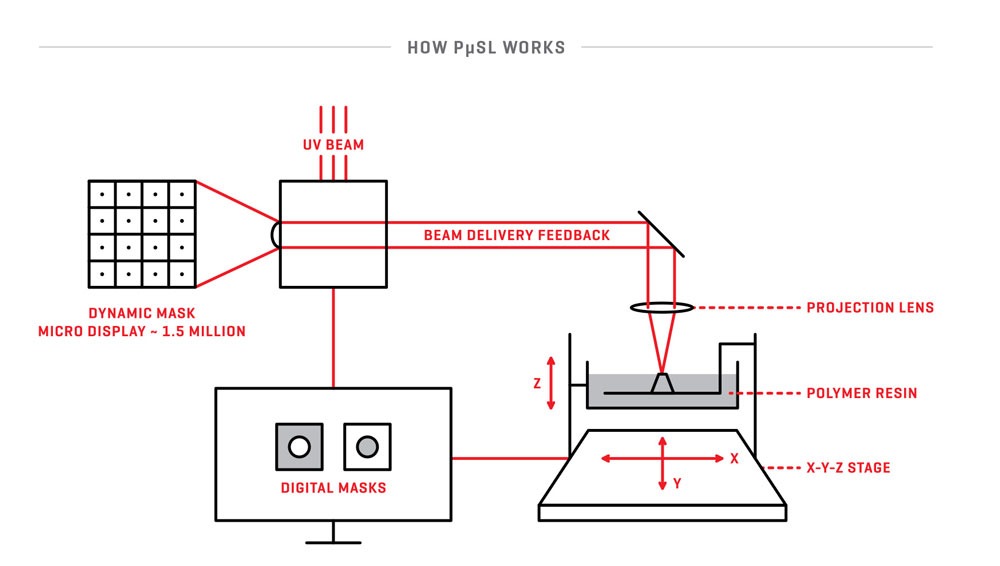
Similar to other 3D printing processes, the process starts with a CAD file that is sliced into a series of 2D images called digital masks that show or hide specific areas of the layer. A 3D structure is then built up layer by layer. As each layer is laid down, it is photopolymerised using a flash of UV light projected into a DLP (Digital Light Processing) chip according to the layer’s mask pattern. By controlling the projection lens, PµSL technology can achieve resolutions from several micrometres or hundreds of nanometres.
BMF’s range of microArch 3D printers use the PµSL process which suits UV-curable materials such as polymers, hydrogels and composite resins that contain ceramic or metal particles. While the open platform allows the use of any (suitable) material, BMF have a range of polymers that offer rigidity, toughness, high-temperature resistance, biocompatibility, flexibility or transparency.
Advantages of the PµSL process include:
- High precision
- High resolution – down to 2µm
- High accuracy
- Excellent surface finish
- No need for moulds or tools
- Can reduce time from concept to prototyping to low volume production
Boston Micro Fabrication 3D printers that utilise PµSl technology. The benchtop microArch S240 with 10µm printing resolution (left) and microArch S230 with 2µm printing resolution (right).
PµSL vs Competing Technologies
PµSL is one of a number of available microfabrication technologies. In comparison, it offers unrivalled resolution, size and tolerance at relatively high speed. Although 2PP-DLW offers higher resolution, resolution of this level is not always required. 3D printing techniques lends them to rapid prototyping, reducing concept to prototype timeframes as well as time to production.
Table 1. Comparison of 3D printing technologies.
Technology | Highest XY Resolution | Speed | Comments |
---|---|---|---|
PµSL | 2 µm | Fast | Fast + high-precision |
SLA | ~50 µm | Slow | Slow + medium precision |
2PP-DLW | <50 nm | Extremely slow | Ultra-high precision, small overall size but very slow |
FDM | ~200 µm | Slow | Rough surface & low precision |
Polyjet | 600 DPI (42 µm) | Fast | Low precision, fast & large size |
Note – 2PP-DLW = 2 photon polymerisation using direct laser writing.
Compared to traditional techniques like micro injection moulding and micro CNC machining, PµSL does not require specialist tools or custom moulds, with the latter often being very expensive and time-consuming to produce. These traditional processes, in particular micro injection moulding are also not well suited to prototyping, especially where a design may still need to be refined and will require large production runs to become economically viable.
Applications of PµSL 3D Printed Parts
The PµSL microfabrication process is suited to production of parts for a wide range of applications. Some of these are summarised in table 2.
Table 2. Examples of applications that can utilise components produced using PµSL.
Industry | Components |
---|---|
Electronics | Connector bases, chip sockets |
Medical devices | Cardiovascular stents, blood heat exchangers, spiral needles |
Microfluidics | Valves for gene sequencing, lab-on-a-chip (LOC) devices |
Filtration | Micro filtration |
Micro-electro-mechanical systems (MEMS) | Micro switches, gears, latches, sensors, motors, valves, actuators, consumer electronics, accelerometers |
Bio-MEMS | Stents, micro needles, LOC devices |
Optical | Optical sensors, optocouplers, fiberglass connectors |
Research | Drug discovery |
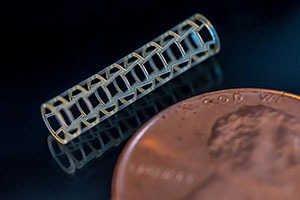
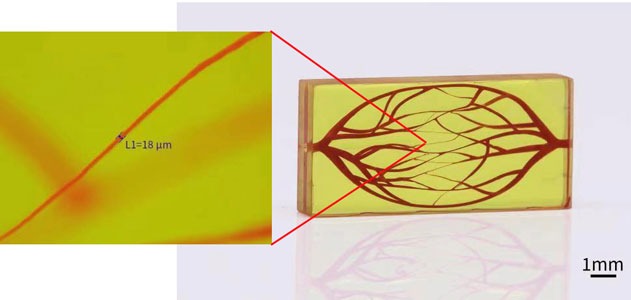
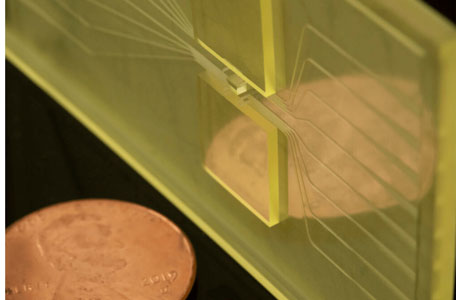
Examples of components that have been micro fabricated using PµSLtechnology. (a) Cardiovascular stent, (b) microfluidic with complex capillary structures as small as 18µm wide and (c) micro mould for producing multiplex microfluidic devices that can be used in the fight against COVID-19.
Summary
3D printing is gaining momentum as a commercial production process, especially in Australia where high value added, with lower volume production is more viable. It is often preferable to more conventional techniques, and the only viable option when components have complex geometries and containing features such as internal cavities which cannot be machined or moulded. Furthermore, with a trend towards miniaturisation, micro fabrication becomes an attractive solution and Projection micro stereolithography (PµSL) becomes an attractive proposition as an ultra-high resolution 3D printing technique that also brings high-speed production, accuracy and precision.